3D finishing of metal additive components
Background and goals
The research focuses on understanding geometric inaccuracies in metal additive manufacturing (AM). Although AM offers design freedom, challenges in achieving high precision persist. The study aims to validate the effectiveness of simulation tools for predicting dimensional accuracy and defects, integrating both additive and subtractive manufacturing processes. This research supports completing the author's doctoral studies.
Objectives and benefits
Investigate residual stresses in AM components.
Assess geometric distortions from subtractive manufacturing (SM).
Develop predictive models integrating AM and SM.
Validate simulation accuracy, enhancing manufacturing reliability and reducing material/energy waste.
Results
The research aims to quantify geometric deformations in metal components manufactured by powder bed fusion, helping to develop more accurate simulations and allowing designers to anticipate defects, ultimately leading to resource savings.
Societal impact
By optimizing AM and SM processes, the research promotes sustainable manufacturing, reducing material waste and energy consumption, thus contributing to environmental conservation and industrial efficiency.
Abstract
This research addresses the challenges of achieving geometric accuracy in metal additive manufacturing (AM). The study aims to validate simulations predicting residual stresses and deformations in additively manufactured components. By combining AM and subtractive manufacturing (SM) techniques, the research develops predictive models for improved precision. Utilizing 5-axis machining and advanced simulations, it seeks to enhance efficiency, reduce material waste, and contribute to sustainable manufacturing practices. The results will support the completion of the author's doctoral studies, with broader implications for industrial applications.
Sustainable development goals
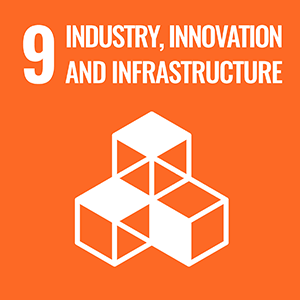